THE BUILDING CONSTRUCTION PROCESS FROM START TO FINISH
THE BUILDING CONSTRUCTION PROCESS FROM START TO FINISH
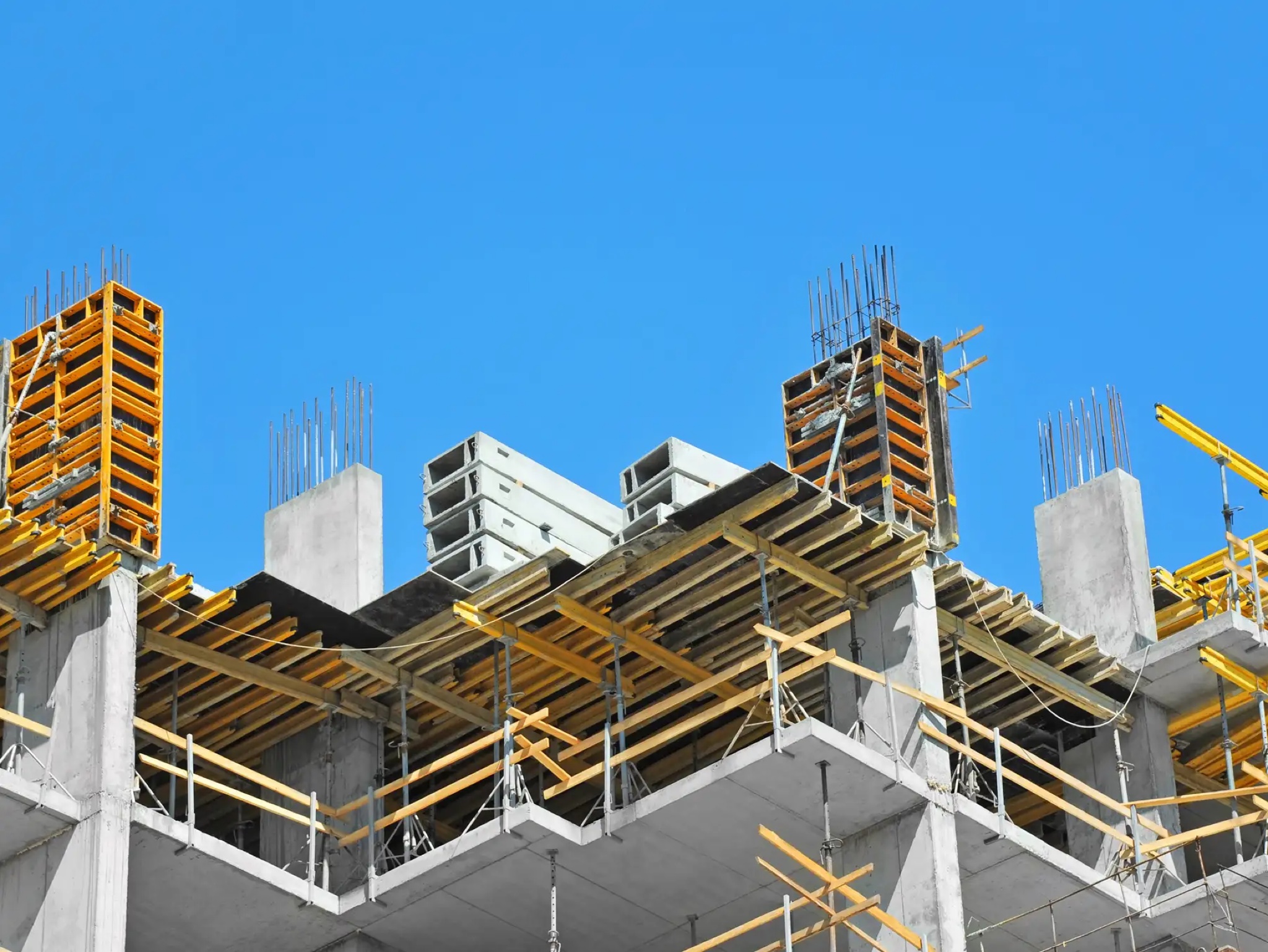
THE BUILDING CONSTRUCTION PROCESS FROM START TO FINISH
BUILDING & CONSTRUCTION
If you’re considering building your dream home, understanding the nuances of construction loans is essential. Unlike traditional home loans, construction loans, also known as owner builder loans, provide a unique financial solution tailored to the building process. These loans grant you access to funds at critical stages of your project, known as progress payments, and you’ll only pay interest on the amount you’ve drawn.
This translates to smaller initial repayments that gradually increase as your construction advances. With variable interest rates and a maximum Loan to Value Ratio (LVR) of 95%, our experienced Property Finance Advisors can help you navigate the lending landscape and ensure your construction journey remains on track, even if your timeline extends up to 6 months.
READ MORE TO KNOW MUCH STEP AND IT EXPLAIN
Although many buildings look similar at first glance, the underlying materials affect their cost and durability — especially in an emergency. Building codes classify all structures from Type 1 to Type 5, and this building type reveals crucial information such as fire resistance.
Some modern buildings have become stronger and cheaper to build. However, manufactured materials like engineered lumber and synthetic plastics burn easily, leading to fast collapses and additional hazards for firefighters.
The most fire-resistant buildings, Type 1 structures, are constructed with concrete and protected steel, which can withstand high temperatures without collapsing. By contrast, Type 5 structures, the least fire-resistant, are lightweight and made of combustible materials that collapse soon after catching fire.
In this post, we will cover all five construction types:
Type 1: Fire-resistive: High-rise buildings made of concrete and protected steel
Type 2: Non-combustible: Newer buildings with tilt-slab or reinforced masonry walls and a metal roof
Type 3: Ordinary: New or old buildings with non-combustible walls but a wood-framed roof
Type 4: Heavy Timber: Older buildings made from thick lumber
Type 5: Wood-framed: Modern buildings with combustible framing and roofs
Read on to learn more about the five building construction types.
Type 1: Fire-resistive
Type 1 buildings are fire-resistant high-rises. Generally, these buildings are more than 75 feet tall, including high-rise housing and commercial spaces. Because of their materials and design, Type 1 buildings are considered the safest in case of a fire, as they are able to withstand high temperatures for long periods of time.
When firefighters encounter Type 1 buildings, they must secure stairwells to ensure a safe evacuation.
Here’s what you should know about Type 1 buildings:
Materials: These buildings are made from reinforced concrete and protected steel covered in a fire-resistant coating.
Strengths: All structural materials are non-combustible, fire-resistant for up to four hours and not vulnerable to collapse.
Weaknesses: Exposed steel can wear down over time and difficult-to-penetrate roofs and windows can prevent ventilation in case of fire.
Special notes: Some Type 1 buildings have specialized HVAC systems and self-pressurizing stairwells that mitigate fire spread.
Overall, Type 1 buildings are highly durable and unlikely to collapse if a fire occurs.
Type 2: Non-combustible
Many new or recently renovated commercial structures — including big-box stores and large shopping malls — are Type 2 buildings. While these buildings generally have fire suppression systems, they are prone to collapse when flames expose their metal roofs to high temperatures.
When firefighters encounter these structures, their main priority is to ventilate the building to prevent flashover, a sudden and dangerous rise in temperature.
Here’s what you should know about Type 2 buildings:
Materials: Walls are either tilt-slab construction or reinforced masonry, both fire-resistant. The metal and lightweight concrete in their roofs are non-combustible, but flammable materials like foam and rubber may be present.
Strengths: They have one to two hours of burn resistance, depending on the materials used.
Weaknesses: Without sufficient ventilation, temperatures can quickly rise, leading to collapse.
Special notes: Firefighters aim to ventilate these buildings with skylights or roll-up doors on the exterior of the building.
Type 2 buildings include many non-combustible materials but still pose risks due to their increased chance of collapse.
Type 3: Ordinary
Schools, businesses and houses with non-combustible walls and wood roofs distinguish themselves as Type 3 buildings. While older buildings tend to have conventionally framed roofs, newer buildings offer lightweight roof systems.
As firefighters approach Type 3 buildings, they prioritize determining whether the building is old or new to make appropriate ventilation decisions.
Here’s what you should know about Type 3 buildings:
Materials: The walls are made from non-combustible tilt-slab or reinforced masonry, while their wooden roofs are flammable.
Strengths: With a combination of non-combustible masonry and fire-cut joists, exterior walls can stand even if the floors collapse.
Weaknesses: Many buildings of this type have connected attics or horizontal void spaces, enabling flames to spread unless fire stops are installed.
Special notes: The roof systems in these buildings — including parallel chord trusses and panelized roofs — determine what types of cut firefighters must make to ventilate the structure.
Although Type 3 buildings contain materials resistant to fire, their roof systems quickly burn and their fire-cut joists pose hazards to firefighters.
Type 4: Heavy Timber
Many Type 4 buildings were constructed before the 1960s using large pieces of lumber. Easily recognized by firefighters, these buildings feature wooden walls and roof spans seen on barns, factories and old churches. They owe their robust structure to lumber connected by metal plates and bolts.
Our website has gone through a research of a building construction process which we provide you the guidelines of building complete guide that should be in the process when building a project or a reel estate project 9jahitsongs is one of the best most amazing entertainment platform that delivered latest worldwide news
While their material is combustible, they fare surprisingly well during fires thanks to the sheer size of the lumber.
Here’s what you should know about Type 4 buildings:
Materials: Large pieces of lumber form these buildings’ walls and roofs.
Strengths: Many load-bearing walls are non-combustible, and their drainage systems allow firefighters’ water to leave the building without increasing weight and risking collapse.
Weaknesses: Metal joints break at high temperatures, and in factories, hazards like oil, machinery or goods can increase fire severity.
Special notes: Though large dimensional lumber holds up well in fire, older buildings with termites or weather damage face an increased risk of collapse.
Although well-maintained Type 4 buildings hold up against fire, the age of some of these buildings poses significant difficulties to firefighters.
Type 5: Wood-framed
Many modern homes fall into Type 5 due to their use of combustible materials — usually wood — in the walls and roof. Unlike the lumber in Type 4 buildings, Type 5 structures use lightweight or manufactured wood. While this material is inexpensive, efficient and structurally sound, it is not fire-resistant and these buildings can collapse minutes after a fire starts.
Firefighters can efficiently ventilate Type 5 buildings because of their wood-framed roofs, but the risk of collapse or flashover is very high.
Here’s what you should know about Type 5 buildings:
Materials: They’re made with wood, often manufactured, or other combustible materials in the walls and roof.
Strengths: Larger beams offer structural support that helps prevent building collapse, and interior platforms often prevent the fire from spreading vertically.
Weaknesses: Manufactured wood burns quickly, and modern construction methods leave buildings at high risk of catching fire.
Special notes: Drywall briefly protects structural elements, but other materials common in this type of construction will fuel fires.
Overall, Type 5 buildings have few fire-resistant properties. While these structures revolutionized the construction industry, they present new difficulties to firefighters.
The Importance of Construction Types
Knowledge about construction types is vital for firefighters and anyone in the construction industry.
Construction workers must understand how different materials and construction techniques affect a building’s resilience to fire, earthquakes and hurricanes. Just as workers should prepare for accidents during construction, they should learn how their work contributes to the future safety of the building.
Firefighters should quickly recognize construction types to form a plan of attack. Understanding how fire spreads in different buildings enables firefighters to make crucial decisions about ventilation and water. Additionally, knowing the construction types saves lives by helping firefighters anticipate dangerous situations like flashover, back draft and collapse.
Construction Types FAQs
Understanding these construction types gives any construction worker or firefighter baseline knowledge about how these structures come together. However, there are additional details about construction types they need to keep in mind. Common questions include:
What Is the Difference Between Type A and Type B Construction?
All construction types except for Type 4 fall into one of two subcategories: Type A or Type B. Type A buildings are “protected” constructions and Type B structures are “unprotected” constructions. Protected constructions are more fire-resistant than unprotected constructions. Type 4 buildings are excluded because of their old age and more uniform design.
What Are the Different Types of Construction Projects?
In addition to the five construction types, there are a few types of construction projects. These include residential buildings, commercial buildings, industrial complexes and heavy civil construction.
What Is “Ordinary Construction?”
Buildings with “ordinary construction” have non-flammable exterior bearing walls with combustible roofs, floors and interior walls.
How Are Fire Resistance Ratings Measured?
Fire ratings are calculated in hour-long intervals. Unlike building types, fire ratings aren’t determined by their basic design. Instead, they take a building’s overall fire resistance into account. For example, a building with a two-hour rating can resist significant damage and collapse caused by fires for at least two hours.
Learning about the different construction types promotes safety during and after a building’s construction. When you’re ready to build your next structure, get the equipment you need online.
READ MORE ON FULL STEP BY STEP BUILDING CONSTRUCTION AND FQ BELOW
Building construction is an ancient human activity that began purely from a functional need to provide shelter from the elements. Over time, human beings have adapted to a variety of climates. The first human shelters were basic structures that did not last long.
Now, more durable structures are available thanks to the development of durable construction materials, elaborate building techniques and processes, and improvements in construction labor.
Building construction is a complex undertaking, irrespective of the type of building. Succeeding requires a lot of time, effort, and financial investment. The first step to a successful construction project is to develop an extensive plan.
The building construction process must be done step by step to ensure an efficient construction process. Consider important aspects such as the purpose of the building, finances, utility, and demand for work before starting the planning phase.
This article will discuss the building construction process from start to finish.
TABLE OF CONTENTS
What is building construction?
Step 1: Pre-construction process
Step 2: Building construction phase
Step 3: Post-construction phase
Summary
FAQs
WHAT IS BUILDING CONSTRUCTION?
Building construction describes the physical activity on a construction site that contributes to building or structure construction. This process involves unloading plant, machinery, materials, cladding, fixture, fitting of installations, formwork, and external finish.
The building construction process is a series of routine tasks completed by skilled persons. It involves a lot of time and tedious work and must be managed carefully. This process can be split into three phases: pre-construction, construction, and post-construction.
STEP 1: PRE-CONSTRUCTION PROCESS
Before a project begins, the client must work closely with the design team and contractor to develop the project plan. The pre-construction process is where the contractor and the design team develop detailed drawings, budgets, schedules, and labor projections.
The core team defines the project and prepares cost estimates depending on the client’s budget. The team must also identify potential risks and develop solutions to ensure optimal use of resources.
The pre-construction phase is characterized by deliberate thoroughness to ensure that all potential needs are identified and addressed early. Regular communication between the core project team and the consultants is vital during pre-construction.
ACQUIRING LAND
The most crucial step in building construction is acquiring land for the project. The location should be well-suited for the project requirements. Before the land acquisition, it is best to conduct feasibility studies to ensure the land is strategically located and is free from land-related issues. It is also necessary to evaluate the project’s cost-effectiveness before kickoff.
INITIAL MEETING
The pre-construction phase starts with an initial meeting between the client and the general contractor. The parties can familiarize themselves with each other. It also allows contractors to understand the client’s needs.
The two parties must define the goals and objectives of the project at this stage. The client has an opportunity to ask questions that the contractor must resolve. The contractor must use this meeting to understand the client’s vision and decide whether or not they can execute it.
The initial meeting allows the contractor to determine the scope of work, the feasibility of the project, and the amount of work required. The contractor can then define the project deliverables and outline a schedule.
ESTIMATING AND BUDGETS
Once the initial meeting is completed, the contractor can visit the site and develop a design and layout. Building construction involves a considerable quantity of material and budget, and it is easy for costs to overrun. Once the planning and structural detailing is done, the construction estimator shares the details.
The construction estimator estimates the quantity and quality of materials needed. The contractor will then develop a budget that includes estimated costs of labor, materials, machinery, and other requirements. The budget will depend on the quality and quantity of materials needed.
If financial resources are limited, the contractor and the property owner must seek pre-approval loans before construction.
SCHEDULE
Once the project scope is laid out and the contractor has done a site visit, it is time to develop a project schedule. The schedule defines when certain aspects of the work will start and end.
The schedule is typically updated during the project lifecycle to paint a clearer picture of construction timelines. Project scheduling is crucial as it affects overall project costs and profit margins.
STEP 2: BUILDING CONSTRUCTION PHASE
With the project plan and team in place, it is time to clear the site and start building. The building construction phase is where the project comes to life. It is a critical step because it involves multiple working parts and deadlines.
Each contractor and subcontractor must now execute the plan, from site preparation to construction.
SITE PREPARATION
Site preparation is the clearing of the site in readiness for construction. Site preparation clears the way for other remedial or demolition work required before workers start constructing the building.
Site clearing involves removing rubbish, machinery, equipment, and unwanted materials. Some site preparation activities may require approvals. The workers must take care not to destroy any trees that are meant to be protected.
A site waste management plan (SWMP) is essential to ensure materials are managed and disposed of efficiently and legally. The SWMP also outlines the reuse and recycling of materials where possible. Only professional disposal experts should handle hazardous substances like asbestos and contaminated waste.
Site preparation is typically carried out under the main construction contract but can be carried out in advance. Site preparation can also be part of a wider enabling works contract, including soil stabilization, demolition, construction of access roads, and services diversion.
CONSTRUCTION
The construction process begins at excavation and ends once the interior and exterior finishes are complete.
EXCAVATION
Once the site is cleared, it is time for excavation. Excavation refers to the removal of earth to form a cavity in the ground. Small sites may do excavation manually using shovels, picks, and wheelbarrows. However, heavy plant machinery is used in large-scale excavations.
Excavation can be classified according to the material being removed, for instance, topsoil, muck, earth, and rock excavation. It can also be classified according to the purpose: trench, road, basement, and bridge excavation.
FOUNDATION
The cleared and excavated site is now ready for construction, and the foundation can be poured. The foundation is the lower part of the substructure. It transfers the building’s loads to the ground.
The foundation is built according to the architect’s drawings. The drawings determine the foundation’s length, width, depth, size, and type.
Concrete foundations are widely used for building structures. However, the choice of foundation can vary depending on the water table level and soil composition of the location. Soil testing is crucial to determine the bearing capacity of the soil.
Shallow foundations may be adequate for low-rise buildings. However, pile foundations are best for high-rise buildings. Builders will place formworks and reinforcements in the excavated trenches to construct the foundation. The Engineer must monitor the reinforcement works.
FRAMING
Framing is the installation of wood frames and steel beams to support the building. It is a time-consuming but crucial part of building construction as it sets the groundwork for the rest of the building.
MASONRY
Now that the framing is complete, it is time to begin the masonry work. The architect’s drawings will determine the material used: ash brick, concrete blocks, or bricks.
The masons bind the building materials using a cement mortar mix, leaving gas for the doors, windows, and doorways.
ELECTRICAL AND PLUMBING WORK
The specialty contractors are brought in to complete the rough plumbing and electrical work. This process involves installing pipes and wires under the floors, ceilings, and walls.
The electrical and plumbing work is not completed at this stage; only the rough work is done to enable drywall, insulation, and ceiling installation. The point and pipe ends must be left out and finished later with plumbing fixtures and electrical fittings.
This step is important to ensure that electrical and plumbing work is not visible after finishing.
ROOFING
Once the basic structure is done, roofing is installed. Roofing protects the interior from the weather elements, preventing damage and disruptions. The contractors should be brought in to start working on the exterior of the building at this stage.
EXTERIOR FINISHING
Exterior finishing involves plastering the external parts of the building. It also involves external cladding to elevate the house.
HEATING AND COOLING WORK
With a roof and exterior walls in place, it is time to address the heating and cooling needs of the building. This process involves the installation of vents, ducts, heating units, and cooling systems.
INTERIOR FINISHING
The next step is to plaster the internal walls for a smooth finish and install tiles on the floor. Interior finishing also includes installing drywall, ceiling, and insulation. The electrician can also come in and finish the outlets and install the light fixtures.
WOODWORK AND FIXTURE FITTINGS
The construction is almost complete now, and it is time to complete the plumbing fittings in the kitchen and bathrooms. Toilets, cabinets, windows, and doors are fitted too.
WATERPROOFING
Waterproofing is the process of preventing water from penetrating the building. Waterproofing is done to reduce humidity and keep the house dry.
PAINTING
Painting gives the house a beautiful finish and protects it from exposure to rain, dirt, sunlight, and stains. A good paint job can give a building 5 to 10 extra years of life.
STEP 3: POST-CONSTRUCTION PHASE
The post-construction phase is the final process before the building is handed over to the client or owner. The post-construction phase includes completing the punch list items and the final walk-through. A punch list is a document that lists all the contract items a contractor must fulfill to be paid.
THE WALK-THROUGH
Once the construction is complete, the team must walk through the building to confirm that all the project specifications have been met. The contractor and the architect must certify that the building is fully functional.
If the architect is satisfied, they will issue a certificate of satisfactory completion. The relevant supervisors must confirm that the building meets the local authorities’ requirements, and the local government will issue a certificate of occupancy.
HANDOVER
The contractor can now hand over the building to the owner. The owner is given substantial time to confirm that they are comfortable operating every aspect of the new building. The contractor can provide training and support as necessary.
The contractor also must hand over all the blueprints and operation manuals to the owner.
SUMMARY
The building construction process is essential to the success of any construction project. It consumes a lot of time and resources but ensures no stone is left unturned.
The building construction process can be split into three main phases, pre-construction, construction, and post-construction. The three main phases of construction involve many systematic activities.
The pre-construction phase includes acquiring land, strategic design, preparing budgets and estimates, acquiring licenses and permits, and hiring experts. The construction phase involves site preparation, excavation, foundation, framing, masonry work, roofing, interior finishes, and exterior finishes.
Finally, post-construction involves the final walkthrough and the handover of the completed building.
FAQS
WHAT IS THE BUILDING CONSTRUCTION PROCESS FROM START TO FINISH?
The building construction process starts from pre-construction, construction, and finally, post-construction. Each of these phases involves different activities.
WHAT IS THE CONSTRUCTION PROJECT CYCLE?
The construction project cycle begins from strategic definition and design to construction and then handover.
WHAT IS THE ORDER OF CONSTRUCTION?
Construction order refers to the major sequence of work followed while constructing a building. Construction order typically starts with marking, excavation, foundation, framing, brick masonry, roofing, flooring, and finishing. All these steps include several activities.
Related news THE BEST 25 BIGGEST SOFTWARE COMPANIES IN THE US
Check out THE 9 BEST ACCOUNTING SOFTWARE FOR FREELANCER IN 2024
WHAT IS THE FIRST STEP OF BUILDING CONSTRUCTION?
The first step of building construction is ensuring the ground is cleared and graded properly. The next step after preparing the land is pouring the foundation. The type of foundation is determined by the type and size of the building.
The skeleton is then created through framing. The walls and windows, doors, and fittings are installed. The electrical and plumbing are done Next. The roof is put up, and the finishing is done.
CHECK OUT HOW 10 STORY BUILDING WAS BUILD IN JUST 45 MINUTES
in this news we will also show you how a 10-story building built in just 28 hours, 45 minutes
Broad Group, a Chinese manufacturing company constructed a 10-story apartment building in just over a day, or 28 hours and 45 minutes, to be exact, and made a splash on the internet for Broad Group.
The residential building is earthquake-resistant and can also be disassembled and moved to another location.
Most trending 9jahitsongs music [TRENDING MUSIC SKALES AS I WAKE UP LYRICS]
Check out [DOWNLOAD LATEST MUSIC] PRINCE G,O,K FT GBSON HUSTLE MP3
Check out LEGACY BOSS FT MANIK SEE SOMETHING SAY SOMETHING
Building and skyscraper construction is a task that frequently takes months or even years, but not for this Chinese construction company in Changsha, a Chinese firm with multiple verticals, one of which is sustainable development.
Some pictures of the construction in Changsha China, were posted by the building’s developer and they instantly went viral.
The project was completed in 2021 by the real estate company using prefabricated construction systems. Trucks were used to deliver each component to the construction site after the rooms and other building modules were prefabricated in a factory.
The Living Building “is endowed with the world’s highest quality in construction,” and it costs the least when it comes to both construction and energy usage. In addition to public buildings, Broad Group thinks the construction process might be utilized to construct buildings up to 200 floors high.
Check out SOLOCVIBEZ BIOGRAPHY REAL NAME STATE OF ORIGIN AND NET WORTH
Back in 2012, the company announced intentions to construct the world’s tallest building in Changsha, which would have been built using prefabricated techniques. Sky City was scheduled to be built in just nine months.
The project was never completed due to safety concerns and a lack of government consent. Local towns have repurposed Sky City’s abandoned foundations into a fish farm.
GET LATEST BALDING CONSTRUCTION PROCESS AT 9JAHITSONGS OUR WEBSITE PROVIDE AND DELIVER MOST LATEST BUILDING PROJECT PROCEE TO MAKE IT EASIER
SHARE NEWS TO SPREAD LOVE
2SLIZ ASSIGNMENT FT G I G GANGZ
SPYRO SHUT DOWN LYRICS FT PHYNO
CHRIS BROWN HMM LYRICS FT DAVIDO
PROMOTE YOUR MUSIC VIDEOS COMEDIES NEWS BIOGRAPHY DJ MIXTAPE AND MANY MORE TODAY WITH US
Do you find 9jahitsongs useful? Click here to give us five stars rating!